How to Work with Predictive Maintenance Data and Why?
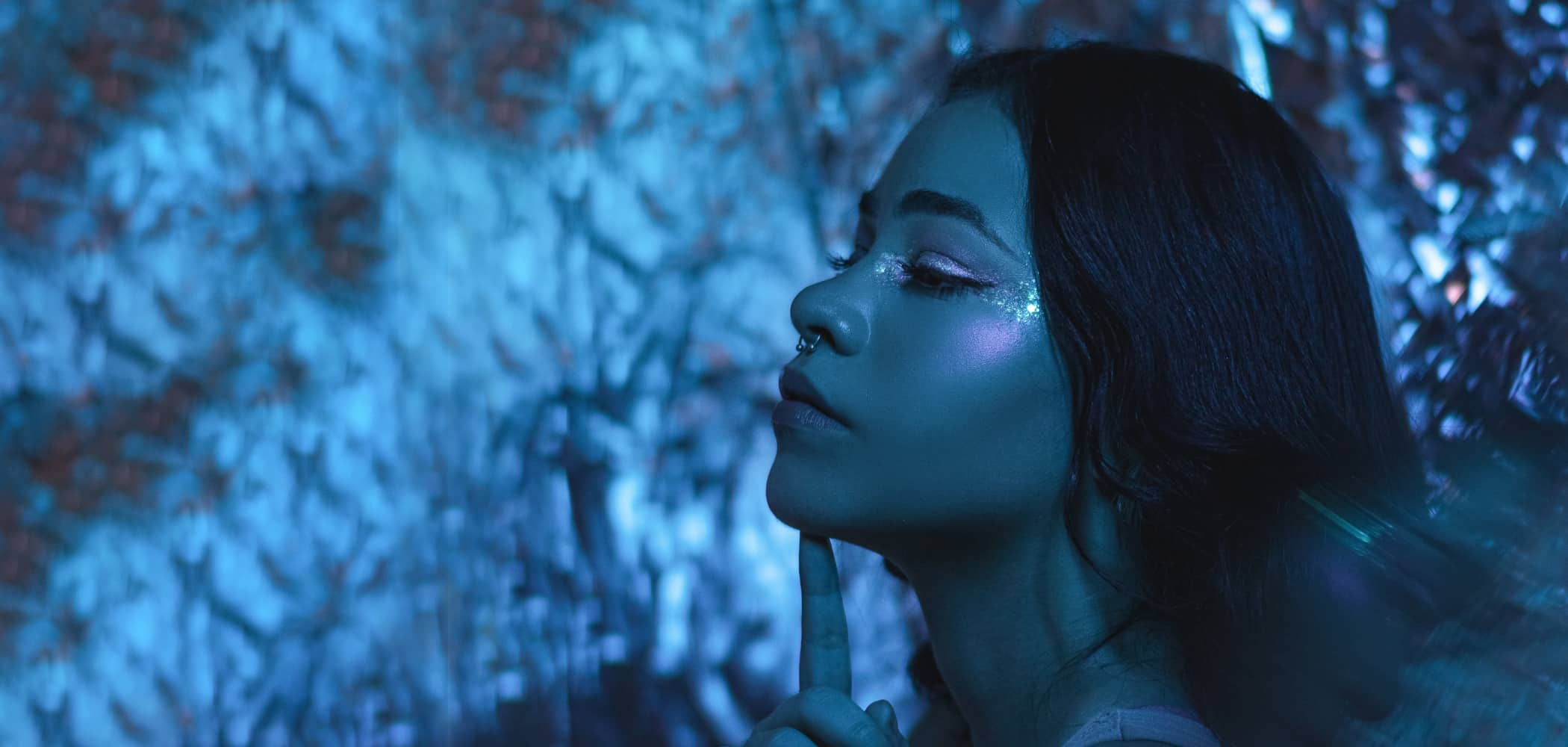
Modern tech-savvy society has reached a tipping point with the most advanced technological innovations known today. Such technological progress provides many solutions that accelerate the growth of the digital culture.
However, tech dependency entails a number of pressing problems, especially for today’s largest manufacturers worldwide. We still can’t avoid the issues associated with keeping such sophisticated machines up and running, aka their maintenance. When an industrial plant is wholly or partly dependent on technology, it becomes imperative to monitor the condition of industrial equipment to prevent production failure. The global machine learning community calls it predictive maintenance.
Most businesses, to date, see predictive maintenance as the most optimal approach to applying industrial data analytics. This is due to the fact that predictive maintenance can reduce equipment downtime by 30%-50% and increase machine life by 20%-40%, as reported by McKinsey. As a result, companies using predictive maintenance data to monitor their machinery should expect to see considerable improvements in their aged industrial infrastructure. So, how exactly does machine learning apply to this data to help industries keep equipment in good condition?
We at Label Your Data tried to collect all the necessary information about predictive maintenance datasets and study how they are applied to the field of machine learning. Read on to find out how ML solutions help modern businesses stay ahead of the curve in adopting state-of-the-art technologies for production purposes and keeping their equipment in a working condition!
Predictive Maintenance Database: What Do You Need It For?
In a nutshell, predictive maintenance, or PdM, is a data-driven strategy that is used to predict when a machine failure will occur. This ML-based method helps estimate when the equipment might fail, pinpoint the problems with the equipment, and identify what parts need to be fixed and when. This way, predictive maintenance algorithms help major industries maintain their tech-dependent, large-scale production by decreasing machinery downtime and increasing its lifetime.
Predictive maintenance has the greatest impact on the following industries:
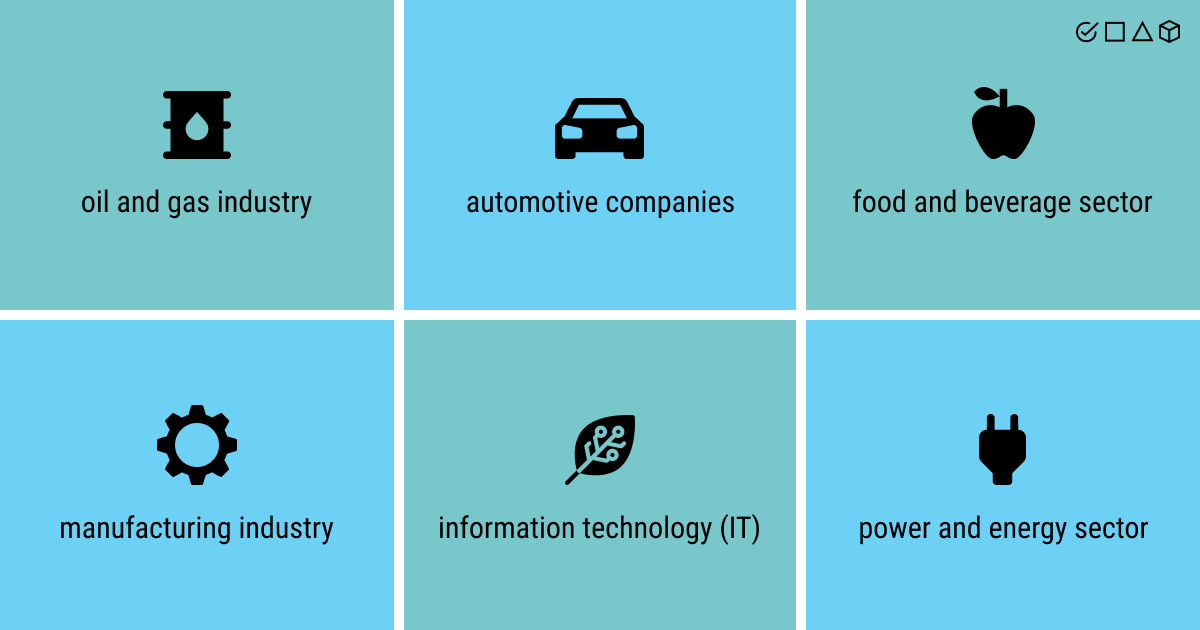
Data is the cornerstone for successful predictive maintenance processes for these industries. The most commonly used types of data in this area include:
- Usage of the asset
- Maintenance history
- Condition of the asset
- Condition data and history of assets from other companies
- Environmental data
Yet, the amount of data (i.e., sensor data) used for predictive maintenance models has grown exponentially. Sensor data, as the name suggests, is collected from smart sensors used on manufacturing equipment and provides information on the current status of a device. Where do companies take this data from, and how do they use it? Most businesses appear to be recognizing the value of data in maintenance once again, since more of them are using a wider range of data sources. Given that predictive maintenance requires sensor data, sensors and instrument inspections are the most frequently used data sources for this sector.
The datasets for these ML models can be obtained from both internal and external repositories. The sensor data for predictive maintenance can be obtained from entire factories, transportation fleets, or infrastructure networks. This data is then distributed via IoT (Internet of Things) sensor technology used in manufacturing.
Machine Learning in Action: An Overview of Predictive Maintenance Workflow
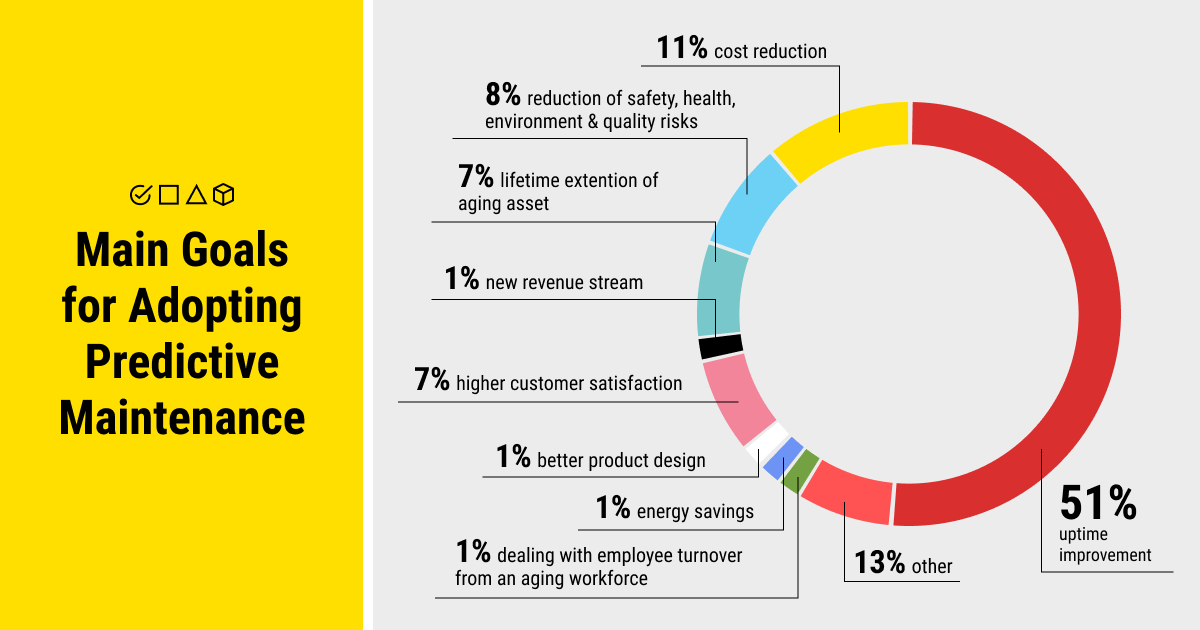
One can easily get overwhelmed with this abundance of data in PdM. But this is when machine learning comes into play to help us make sense of all this data in predictive analytics, and we’ll try to break it all down for you.
What’s the role of ML in industrial settings where predictive maintenance is applied? ML algorithms are particularly important in this regard. These are self-learning algorithms that develop their own model of the world by executing a series of trials on a set of training data and inferring rules. The ML model for predictive maintenance can be refined by adding a new batch of data, thus, improving its predictive capabilities.
It should be noted that self-learning algorithms are designed to improve their own performance. In the field of ML, this means that a large amount of data needs to be analyzed and processed to fuel such a powerful system. If you’re having a hard time with huge volumes of data and need professional help in preparing it for your ML model, contact our team at Label Your Data, so we can handle your data the right way!
Predictive maintenance methods are designed to help maintenance managers and technicians monitor the condition and performance of equipment during normal operation. It’s a proactive strategy aimed at preventing asset failures. With the help of predictive maintenance algorithms, IoT devices, and sensors, it’s possible to forecast when the machine might break down. As a result, large manufacturers can significantly reduce their maintenance frequency, time, and costs, and rather invest it all into production.
But before you start building the predictive maintenance model, you need to set the baselines. One needs to check the conditional baselines of the equipment in service and collect the necessary (conditional) data. This way, you can control the abnormalities. However, it’s important to have the right data on hand to build an effective model and generate accurate results. In predictive maintenance, this means you have to align the predictive maintenance programs with the right condition-monitoring technology, like CMM systems and IoT-enabled devices. The relevant sensors need to be attached to the assets and then connected to the CMMS or remote dashboard, where sensor data is processed by maintenance engineers.
But why does IoT play such a pivotal role in developing an effective maintenance strategy? IoT devices can connect the collected data to predictive maintenance systems. From there, it’s quite simple: when the operation of the equipment deviates from the standard settings, the sensors trigger the predictive maintenance protocol. After that, the work order is monitored through the CMMS and assigned to the technicians who can repair the equipment to address the reported anomaly.
Predictive Maintenance Datasets for Machine Learning
Predictive maintenance datasets generally come in two categories: structured and unstructured. Structured data involves spreadsheets or relational databases, while unstructured data implies maintenance logs or thermal images. External data, required for PdM algorithms, includes environmental data on temperature, humidity and wind speeds, as well as operator profiles or specifications of materials that are processed at the moment of machine failure.
Here’s the list of the most up-to-date libraries providing free datasets for predictive maintenance that we’ve discovered:
- UC Irvine ML Repository
- Google Datasets
- GitHub
- kaggle Predictive Maintenance
- kaggle Bosch Production Line Performance
- Prognostics Data Repository
After you’ve found the necessary datasets or collected the maintenance data yourself, you can use it to build an actual ML model and start implementing a predictive maintenance system. With the right ML datasets on hand, one can easily develop predictive algorithms to build a more complex analytics system to set a maintenance task and schedule it accordingly. Once created, this system will help optimize industrial plant operations by reducing machinery downtime.
How to Build a Predictive Maintenance Model?
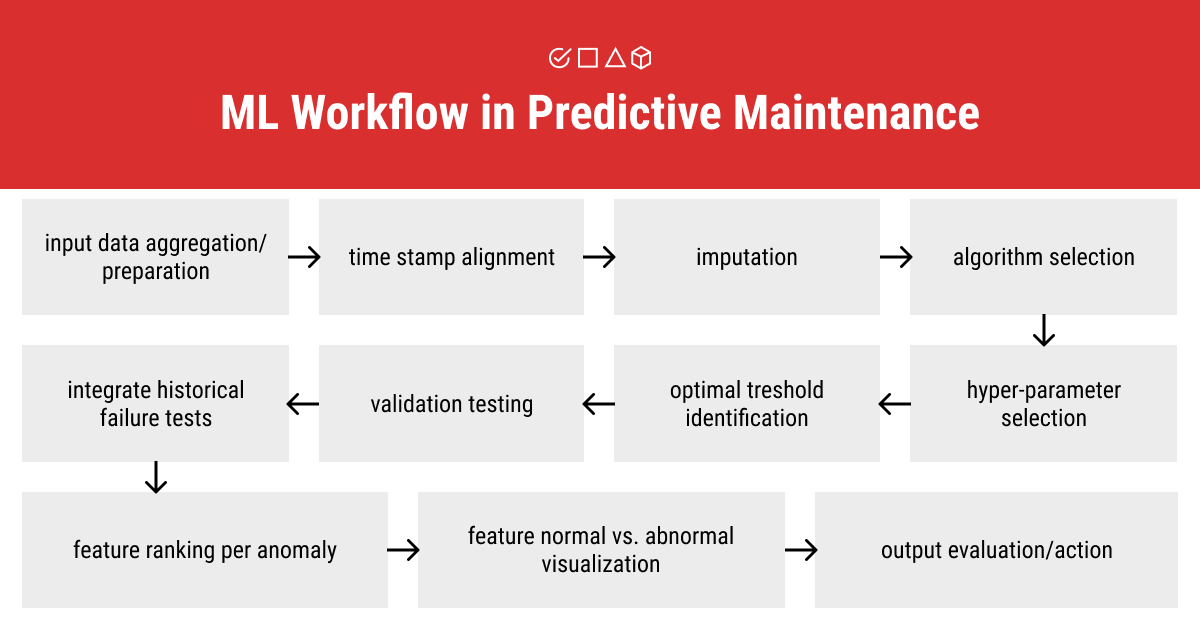
Modern production is already performed by robots that have their own analytics platforms, so they require continuous monitoring and maintenance. Today, most leading industries rely on predictive maintenance solutions for their machinery, which means they keep investing in automation and predictive maintenance-based processes. Companies also see predictive maintenance as the key strategy for developing new products and business models. A deep ML expertise is crucial here.
Building an ML model that captures the relationship between the extracted features and the degradation path of the equipment will help estimate how much time is left before the failure, and when the maintenance should be performed. What steps should one take to build a model for predictive maintenance?
- Collect data: Obtain maintenance data using sensors (collect data under different operating conditions).
- Work with your data: Clean your data by filtering out the noise (extract useful features from raw data, aka condition indicators).
- Identify condition indicators: Use extracted features as condition indicators to differentiate a healthy operation from a faulty one.
- Train your model: Model training using extracted features helps detect anomalies and different types of faults, and predict the remaining service life of the equipment.
- Implement your model: Deploy and integrate an ML model for predictive maintenance, either on the edge device or in the cloud.
- Assess: Evaluate the machine learning model using generated features.
Therefore, a typical ML workflow for a predictive maintenance system covers several steps, where both data and technical expertise synchronize. Despite the complex nature of ML models, especially predictive ones, more and more companies use this strategy to achieve important production goals. They include reduced repair time, unplanned downtime, and extended life of aged industrial equipment.
Choosing the right partner for carrying out such a complex, data-driven process is a key point in a successful PdM initiative. If you have a lot of maintenance data, you need to label it before it’s fed into the model. Reach out to our team of data annotation experts to help you prepare the data for your future maintenance model!
Implementing Predictive Maintenance: A Step-by-Step Guide
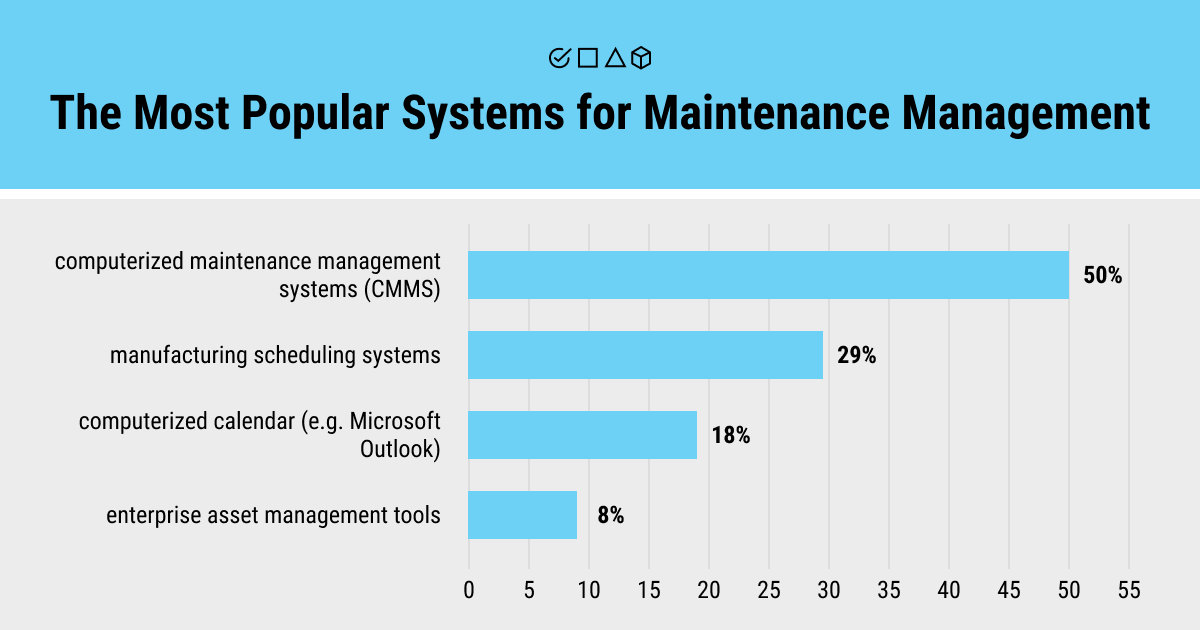
Now let’s get to the fun part: deploying a predictive maintenance system in practice. This strategy is highly important for companies wishing to boost their operational efficiency and optimize the operational costs of maintenance processes. And we can’t stress this enough, but businesses adopt predictive maintenance methods mainly because they can improve the utilization rate of the equipment.
However, there are a few essential factors to consider before developing the final predictive maintenance solution:
— Error history
An ML model for predictive maintenance requires data both on normal operational patterns and failure patterns before it’s trained. Thus, a training dataset should include a sufficient amount of training examples on normal and error samples.
— Maintenance history
This step refers to the detailed information on the machine repairs in the past, which is a crucial component of the predictive maintenance dataset. Otherwise, one risks getting misleading results from the model.
— Machine operating conditions
Another valuable information for the dataset in predictive maintenance is the aging pattern of the asset, given that the condition of machines in production tends to get worse over time as it performs many operations per day. Anomalies should be recorded too to trace the degradation pattern.
— Equipment metadata
Such metadata includes static feature data on the technical information of the equipment in service, like the date of creation, the model, the start date of service, and the system’s location.
Predictive Maintenance with Machine Learning: Examples and Use Cases
More and more businesses today adopt predictive maintenance solutions to reduce repair time and unplanned downtime. This way, they can improve the utilization rate of their assets. But with many solutions come many use cases, and we’ll take a look at some of the most interesting ones.
But before we move on to real-life examples of predictive maintenance, it’s worth mentioning some of the main types of this method to better understand its applications in the business world. The main types of predictive maintenance systems include:
- Infrared Imagery (IR cameras): Hot spots of electric wiring
- Acoustic Analysis: Detecting gas and vacuum leaks
- Vibration Analysis: Determining the fluctuations of the vibration of essential components
- Oil Analysis: Checking the condition of a machine’s oil lubrication system
To get the most use of and properly deploy predictive maintenance systems, organizations can’t do without the help of data scientists. They are an essential link in the chain of ML-based predictive maintenance processes, which is responsible for developing effective predictive models to be further fed with data obtained from the installed sensors.
Keep in mind that these models should always be trained with annotated failure-related datasets. Contact our team if you’re planning on creating your own predictive model and need a set of well-labeled data! Now let’s examine the real-world examples of predictive maintenance:
Amazon
Amazon has launched a few industrial ML services, including AWS Monitron and Amazon Lookout for Equipment. Amazon Monitron is designed for customers who don't have an existing sensor network but require an end-to-end machine monitoring solution to detect abnormal equipment conditions. Amazon Lookout for Equipment is, in turn, created for clients who already have equipment sensors. It enables them to use ML models to identify abnormal equipment behavior and schedule maintenance correctly.
Nestlé
Nestlé has integrated IoT into its corporate coffee machine offering, which serves more than 2,500 of its clients. Here, predictive maintenance allows for remote configuration of the machine and smooth-running maintenance. The older equipment is modified with IoT capabilities as well.
Frito-Lay
The snack food manufacturer and PepsiCo’s subsidiary, Frito-Lay, has a successful track record of launching a sophisticated PdM technology initiative. Predictive maintenance helped the firm reduce planned downtime to 0.75% and unplanned one to 2.88%. This strategy also helped the company enhance its operations in a variety of ways.
Chevron
One of the largest oil and gas corporations in the world, Chevron, has adopted end-to-end production equipment to save costs and implement innovative ML solutions in exploration, midstream logistics, retail operations, and oil wells management across the globe. Predictive maintenance helped Chevron predict when equipment should be serviced with the finest precision.
Benefits and Challenges of Predictive Maintenance
— Benefits
- Minimized risk of unplanned downtime and unscheduled maintenance of equipment
- Increased life expectancy of machines and equipment
- Fewer breakdowns and failures of industrial machinery
- Saved time and costs in terms of labor, spare parts, and equipment
- Increased service life of industrial equipment
- Improved safety throughout the workplace for technicians and operators
However, it requires a commendable effort from the maintenance team to achieve these benefits in predictive maintenance. What it takes is a detailed and time-consuming approach to the planning of the maintenance strategy throughout the production stage, considering all the equipment details. The PdM team also requires costly condition-monitoring equipment for the most efficient predictive results, monitored by a skilled and tech-savvy maintenance team.
— Challenges
- The lack of necessary applications and technical expertise
- Understanding the scope of problems to solve with ML
- Diverse assets and quality of data
- The lack of resources (time, scale, talent)
Summary: Laying The Groundwork for the Digital Industrial Revolution With Advanced Maintenance
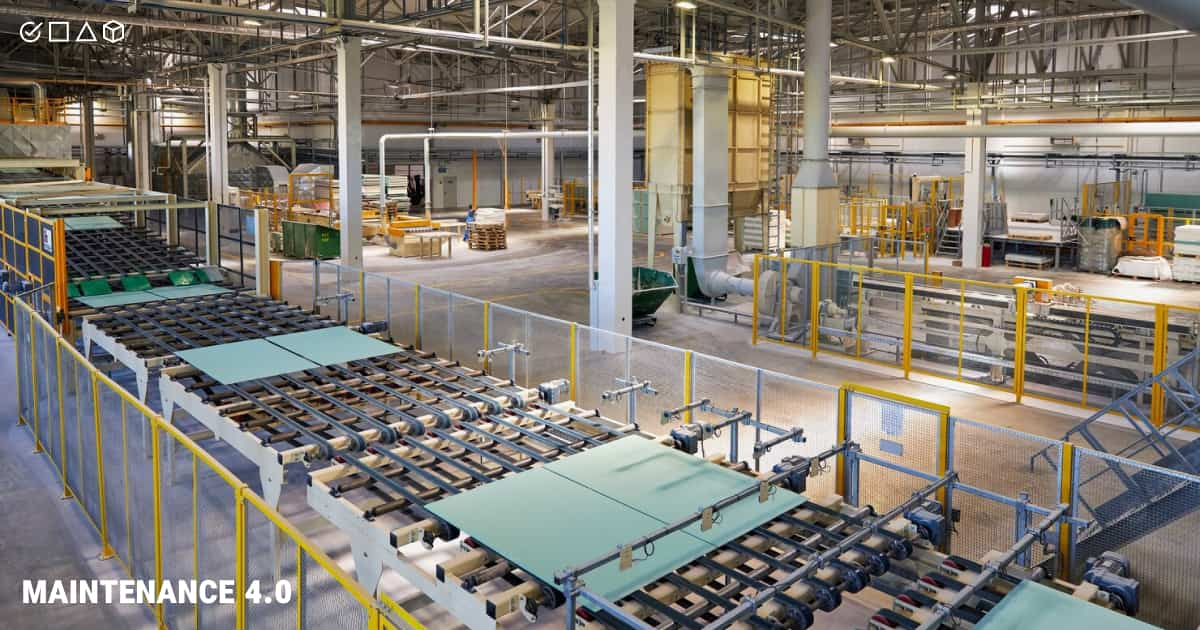
We are witnessing a rising number of companies fall to the current key trend — digitalization. It's the era of the digital revolution for the industries that are becoming increasingly automated and reliant on technology. Such changes in the global labor market indicate that advanced technologies have a significant impact on our lives and livelihood.
The Fourth Industrial Revolution, aka the Maintenance 4.0, highlights the pursuit of a digital culture. The increased use of sophisticated technologies and sensor devices accelerates the development of ML methods that maintain these technologies and ease the work for human workers. So, why does predictive maintenance matter?
For businesses, it’s a guarantee of successful adoption of state-of-the-art equipment, smooth-running operations, and no unexpected breakdowns. It’s also a great time- and cost-saving business strategy. Thus, companies can rely on technology with confidence and concentrate on production. But never forget about data, the core element behind such a complex system like predictive maintenance.
Are you thinking of making your own prediction model? Make sure to enlist the support of true data experts, like we are at Label Your Data. Contact us today and get your quote!
Written by
Karyna is the CEO of Label Your Data, a company specializing in data labeling solutions for machine learning projects. With a strong background in machine learning, she frequently collaborates with editors to share her expertise through articles, whitepapers, and presentations.